- DESCRIPTION
- Datasheet
DESCRIPTION
WHERE TO USE
Mapefloor I 390 EDF is used to form electrically dissipative coatings on concrete substrates and cementitious screeds, including those exposed to medium to heavy traffic. Once hardened, Mapefloor I 390 EDF is characterised by a low release of micro-particles and volatile organic compounds (VOC) into the air. Thus it’s particularly suitable for coating floors in cleanrooms where a high standard of hygiene is required, the dimensions and amount of suspended micro-particles need to be constantly monitored and the presence of potential biological and physical pollutants that could interfere with the various processes needs to be kept under control. Mapefloor I 390 EDF is used in particular to make dissipative coatings in environments like:
▪ electronic industries;
▪ chemical and pharmaceutical industries
▪ laboratories;
▪ hospitals and operating theatres.
▪ automotive and aerospace industries;
warehouses of flammable substances;
▪ sterile environments;
▪ cleanrooms.
TECHNICAL CHARACTERISTICS
Mapefloor I 390 EDF is a two-component, high solid content, pigmented, epoxy resin-based formulate containing electrically-conductive fillers according to a formulation developed in the MAPEI R&D laboratories. Mapefloor I 390 EDF is used to make smooth, self-levelling, waterproof, dissipative coatings with high mechanical strength and good resistance to chemicals. Mapefloor I 390 EDF is applied on substrates after treating their surface with Primer W-AS N, a special twocomponent water-based epoxy primer for electrically conductive dissipative coatings. Mapefloor I 390 EDF is used to make seamless, self-levelling coatings specific for cleanrooms class ISO 3, concerning particle emissions according to ISO 14644-1, and class -7.9, concerning VOC emissions according to ISO 14644-8. Decontaminable according to ISO 8690/1998 with Cs and Co. MAPEFLOOR I 390 EDF Two-component, self-levelling epoxy formulation used to form strong, dissipative coatings 137 60 Mapefloor I 390 EDF complies with the principles defined in EN 13813 “Screeds and materials for screeds – Materials for screeds – Properties and requirements”, which specifies the requirements for screed materials used in the construction of internal floors.
ADVANTAGES
▪ Electrically dissipative.
▪ High mechanical strength and good resistance to chemicals.
▪ Waterproof
▪ Dust proof.
▪ Ease of cleaning and sanitising (Riboflavin test ISO 4628-1).
▪ Fulfills ATEX 137.
▪ Bacteriostatic (ISO 22196).
▪ System fast to put into service.
Datasheet
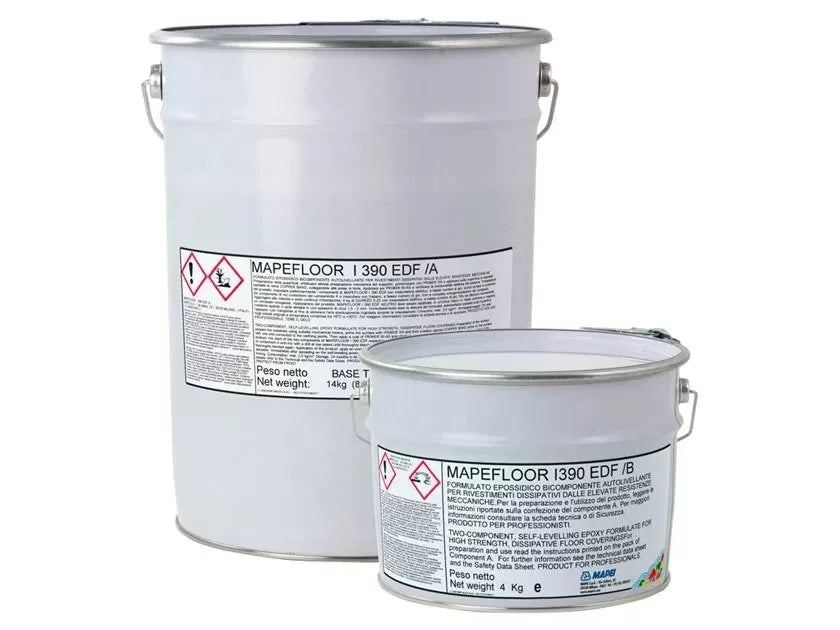