Select Your Colour
- DESCRIPTION
- Datasheet
DESCRIPTION
Description
PPG SigmaCover 400 is a two-component, high solids general purpose epoxy primer for steel and galvanised steel.
Product Features and Benefits
- High performance self priming universal epoxy
- High solids, low VOC
- Surface tolerant and abrasion resistant
- Compatible with prepared, damp surfaces
- Good adhesion on most existing coatings
- Available in MIO or conventional pigmented grade
- Good resistance to splash and spillage of chemicals
- Meets NSF Standard 61 for valves (US manufacturing only)
- Colours: Standard primer colours and custom colours available
- Gloss level: Semi-gloss
Method of Application
- Air spray
- Airless spray
- Brush/Roller
Note:
Epoxy coatings will chalk and fade with exposure to sunlight. Light colors are prone to ambering to some extent. Note that product tinted to custom colors are not recommended for immersion service. Only use factory grind batches for immersion.
Coating performance is proportional to the degree of surface preparation. Remove all loose paint, mill scale, and rust. The surface to be coated must be dimensionally stable, dry, clean and free of grease, oil, and other foreign materials. When proper abrasive blast surface preparation is not practical, surfaces should be chipped clean and wire brushed to bare, clean material.
Application by brush: apply evenly using a clean, well-loaded brush. Application by brush or roller will provide approximately 80 μm (3.1 mils) DFT in a single-coat application.
Please refer to the product Data Sheet for surface preparation, mixing and application instructions.
Primers and Topcoats
Primers
- Dimetcoat Series
- Amercoat 68 Series
- Amerlock 2 / 400 Series
- SigmaZinc Series
- Amercoat Epoxies
- Sigma Epoxies
Topcoats
- Amercoat 450 Series
- SigmaDur Series
- SigmaCover Epoxies
- Amercoat Epoxies
- Amershield
- PSX 700
Please contact us for suitable primers and topcoats for PPG SigmaCover 400.
Note:
A detergent wash with Prep 88 / Sigmarite 88 or equivalent is required prior to application of topcoats after 30 days of exposure.
If maximum recoat time has been exceeded, roughen surfaces.
Alkyd coatings and waterborne acrylic coatings should be applied after the film is dry to handle and not greater than three times dry to handle time.
Maximum recoating time is highly dependent upon actual surface temperature – not simply air temperatures. Sun-exposed or otherwise heated surface will shorten the maximum recoat window.
Thinner
- PPG Thinner 91-92 for global
- PPG Thinner 21-06 (Amercoat 65) for NSF/ANSI 61
- PPG Thinner 21-25 (Amercoat 101) for Non-NSF/ANSI 61 and > 90°F (32°C)
Volume of Thinner
Air Spray
0 – 10% depending on required thickness and application conditions.
Airless Spray
0 – 5% depending on required thickness and application conditions.
Refer to product Data Sheet for further details or contact us for free technical advice.
Cleanup
- PPG Thinner 90-53
- PPG Thinner 90-58 (Amercoat 12)
- PPG Thinner 21-06 (Amercoat 65)
Safety Precautions
- Adequate ventilation must be maintained during application and curing (please refer to Information Sheets 1433 and 1434)
- For paint and recommended thinners see Information Sheets 1430, 1431 and relevant Material Safety Data Sheets
- This is a solvent-borne paint and care should be taken to avoid inhalation of spray mist or vapour, as well as contact between the wet paint and exposed skin or eyes
Please refer to the product Data Sheet and Material Safety Data Sheets for full details regarding the safe use of this product.
Contact Us
For further advice regarding the use of this product, technical support or a quotation please contact us
Datasheet
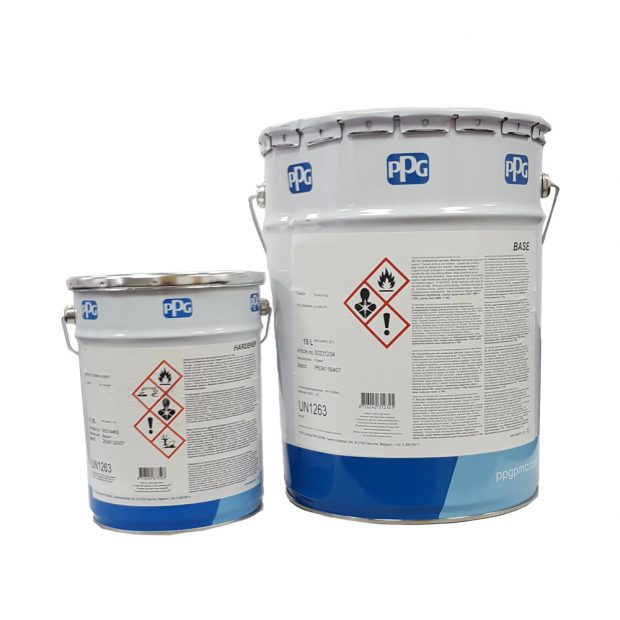
